Point cloud technology brings accuracy and beauty to home construction
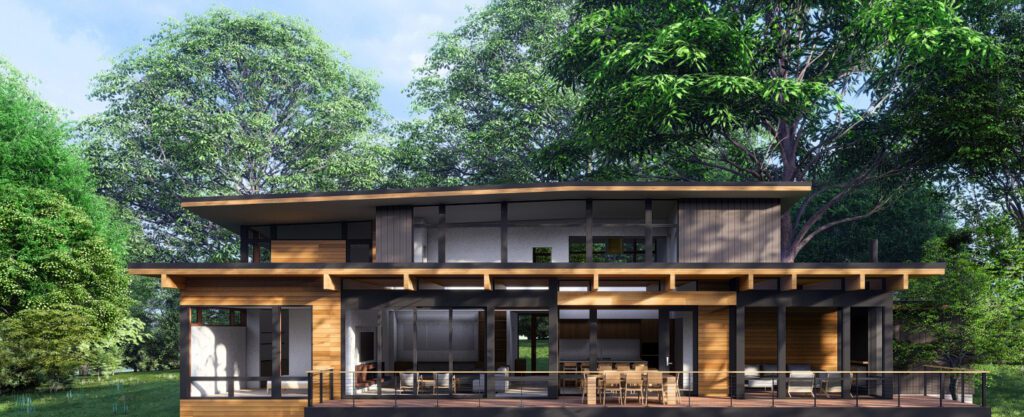
When it comes time to build your custom home, you want to get it right the first time. You need to feel confident that you’ve chosen an architectural practice that prioritizes accuracy and precision alongside inspired design.
At Turkel Design, we have developed a systematized process to ensure that the custom home you fall in love with during the design process is the home that is ultimately assembled on your building site. It’s a process that we are constantly refining and improving thanks to evolving technology. With traditional construction, you might be surprised how often the home that is built does not match what the architect drew—or that the architectural drawings do not represent a buildable structure. Our prefabrication method, on the other hand, employs technological advancements to ensure that the homes we design can be constructed and with greater precision—in less time, at a lower overall cost—than if they were designed and built using traditional methods.
Freed from traditional stick-built construction, we leverage technology to enhance every aspect of the planning and construction process, from 3D scanning, modeling, and visualization, to manufacturing. These tools bring predictability to every building we design and prefabricate, reducing risk and resulting in a more beautiful home.
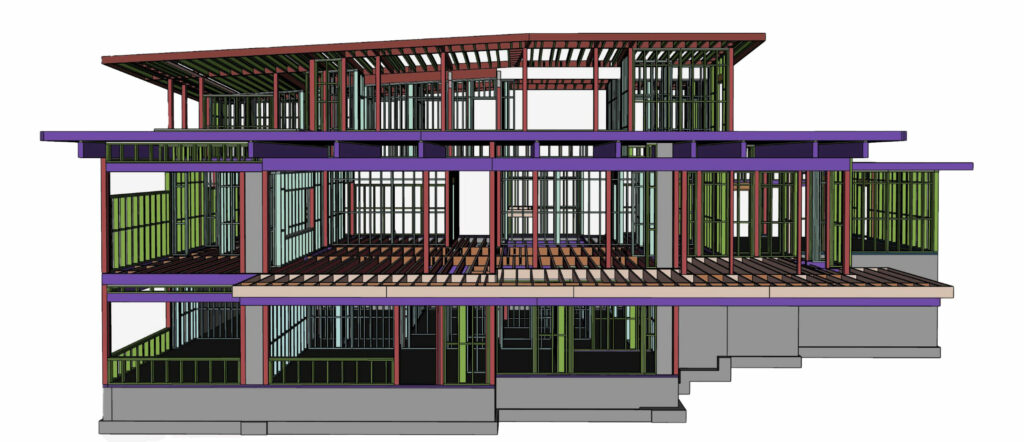
To achieve this predictability, precision is critical. The accuracy of our homes is due not only to prefabrication, but also to the 3D Building Information Modeling (BIM) software, which allows for the resolution of conflicts prior to prefabrication. To supplement our BIM models, we employ 3D on-site scanning technology that eliminates the need for measuring the building by hand. Digital scanning of the foundation, for example, enables our architects to assess the accuracy of the home in real time, during the construction process.
This software allows each design to exist as a collection of data points in a cloud; the spatial relationships between each point reflect the accurate measurements of the home under construction. At the Turkel Design studio in Somerville, Massachusetts, our design team can be confident about the measurements of the foundation of any project, whether it’s in Hawaii or Colorado.
The point cloud data feeds into our BIM, which contains every detail about the building components that are prefabricated in the factory. When the prefab package is delivered to the building site, we can be confident that it fits the foundation that your local general contractor has prepared.
The BIM also provides documentation used by the contractor to assemble the home. At each step of the process, the data is consistent, allowing the architect, the contractor, and any other necessary consultants to collaborate without conflicting information. This consistency reduces the need for revisions and corrections, which saves the homeowner time and money.
Part of the beauty of the point cloud scan is that, through its inherent accuracy, it reduces the possibility of human error that comes with measuring by hand, or entering data into multiple software programs. It clarifies communication between Turkel Design and the local contractor, ensuring that everyone is working from precise information. Because of the sheer volume of data stored in the model, each stakeholder can utilize it to serve their needs. The model can be viewed in any number of ways—it even allows users to virtually walk through the home.
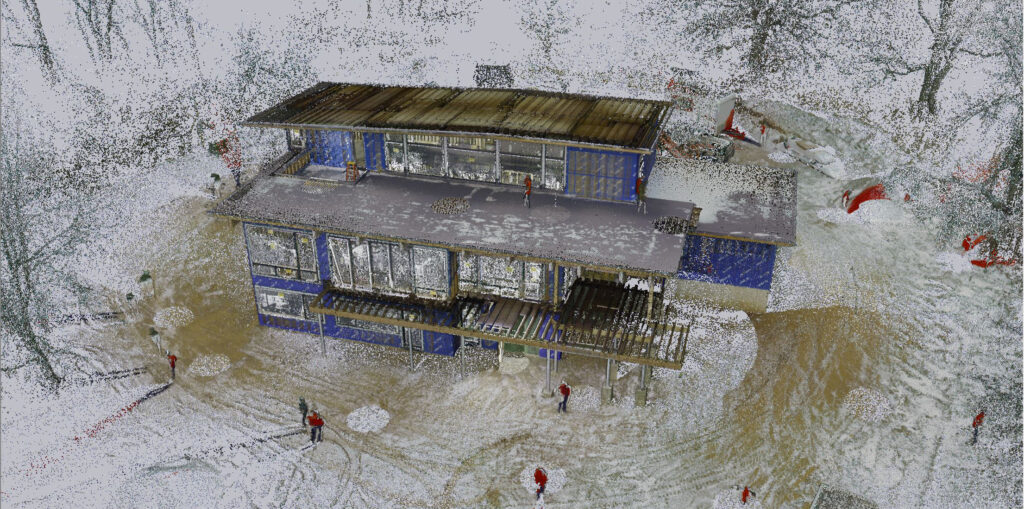
Those who see these images at a glance may not realize the accuracy of the data they contain. For example, a Turkel Design home in Ohio—a variation on our Axiom 2650 design—is nearing completion thanks in part to the road map of data visualized in the image above. In a future post, we’ll move indoors to see how digital scanning and point cloud technology ensure that our custom cabinetry fits beautifully within the home.
Turkel Design is always looking for new methods to improve accuracy and clear communication between stakeholders. Every step of the way—from an initial visit to your building site, through the interactive design process, permitting, fabrication, assembly, and finishing—we have refined our process to reduce risk and bring predictability to the cost, timeline, and quality of your custom home project.
We think there’s beauty in predictability—figuratively and literally. This principle informs the process behind our modern custom homes.
If you want to design and build a custom home but are worried about the risks involved, please contact us to learn more about our unique approach to reducing those risks. We can design a home specifically for where and how you want to live—using a forward-looking process that’s as elegant as the result.